CNC Mill vs CNC Router: Beginner’s Guide to Selection
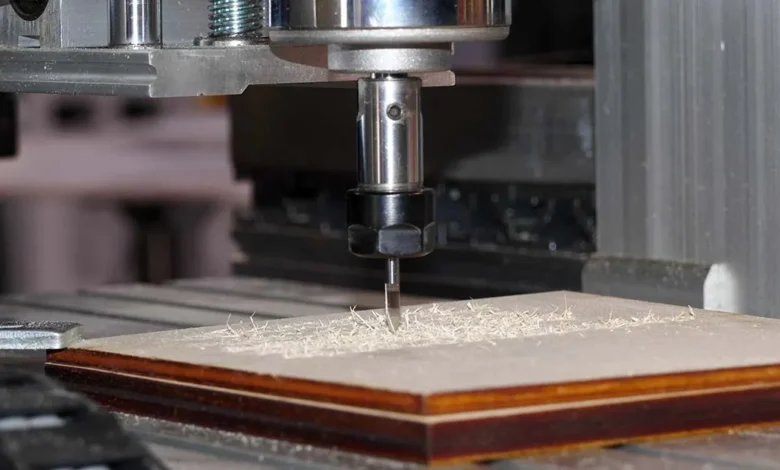
Choosing between a CNC mill and a CNC lathe (CNC turn) can be overwhelming for beginners. Both machines offer precision machining like a typical CNC technique but operate differently. Therefore, machinists must consider project requirements, budget, skill level, and long-term goals before selecting the better option.
This guide breaks down key considerations, practical tips, and essential factors to help beginners make an informed decision. Whether investing in your first CNC machine or outsourcing machining services, understanding these fundamentals is crucial for efficiency and success.
CNC Mill vs CNC Turn: A Beginner’s Guide to Choosing the Right Machine
CNC milling vs turning are two fundamental machining processes that cut and shape materials with high precision. Milling involves a rotating cutting tool that removes material from a stationary workpiece, making it ideal for complex geometries, pockets, and intricate surface finishes. On the other hand, turning uses a single-point fixed cutting tool while the workpiece rotates, making it better suited for cylindrical parts like shafts and bushings.
Understanding these core differences is essential for beginners. CNC milling allows for greater design flexibility, handling intricate parts with multiple features. However, depending on design complexity, it requires more tool changes and programming expertise. In contrast, CNC turning is generally more efficient for symmetrical parts and often faster for high-volume production, but it is limited in creating non-cylindrical shapes.
Newbies and machining enthusiasts should also consider machine setup and operation. CNC mills often demand more complex fixturing and multiple axes, while CNC lathes provide a simpler setup with fewer tools. The learning curve matters, too—milling typically involves advanced CAM programming, whereas turning is relatively easier to grasp.
Key Factors to Consider for Beginners
Choosing between a CNC mill and a CNC lathe (turning machine) isn’t just about the machine itself—it depends on several crucial factors that impact efficiency, cost, and overall usability. Beginners should first analyze their projects’ needs before considering other elements like budget and skill level.
Below are key factors to evaluate when making the right choice.
Type of Parts and Project Requirements
The first and most important factor is the nature of the parts to be produced. CNC mills are better suited for complex geometries, flat surfaces, and pockets, whereas CNC lathes excel in cylindrical and rotationally symmetric components. However, some projects may require a combo of milling and turning operations; in such cases, a CNC mill-turn hybrid might be necessary.
Budget and Investment Considerations
CNC machines are generally expensive because of their sophistication. Due to their complexity, suitability for more extensive machining solutions, and tooling requirements, CNC mills are usually more costly. While CNC lathes are generally more affordable than mills, they also require significant investment. However, lathe machines may still need extra tooling to ensure its versatility. Therefore, beginners must factor in the machine cost and tooling, maintenance, and software expenses.
Skill Level and Training Requirements
CNC machines require extensive solutions to program, troubleshoot, and maximize their capabilities. However, because of their increased sophistication, CNC mills may require more extensive training than lathe machines. CNC mills may involve multi-axis movements and complex tool paths. Therefore, CNC turning is relatively easier for beginners due to its more straightforward motion control. Those with limited CNC experience may find lathes a better starting point before progressing to more intricate milling operations.
Production Volume and Efficiency
CNC turning can be more efficient for high-volume production due to faster cycle times for cylindrical parts. However, CNC milling is better for low-to-medium production runs where customization and precision are key.
Machine Flexibility and Future Expansion
Beginners should consider whether they need a specialized or versatile machine. We cannot overemphasize CNC mills’ ability to perform various operations, including drilling, contouring, and slotting, which makes them more flexible. In contrast, CNC lathes have a limited scope but can integrate with live tooling for added functionality.
Support, Software, and After-Sales Services
Lastly, access to training, technical support, and user-friendly software plays a significant role. Therefore, newbies should opt for machines with strong manufacturer support, comprehensive manuals, and compatible CAM software to ease the learning curve.
With all that we have discussed, CNC lathes may be a better option for beginners, as they are relatively more straightforward to operate. However, you must still consider if it’ll benefit you in the long run. Therefore, the reason to factor in your project’s needs, specialization, and if it even suits your intended fabrication.
Practical Tips for New Users
For beginners stepping into CNC machining, mastering a CNC mill or lathe requires more than just understanding machine differences. It also involves preparation, hands-on practice, and leveraging available resources.
Below are practical tips to help new users start efficiently and avoid costly mistakes.
Start with Simple Projects
As a general rule, newbies should start from the known to the unknown. Therefore, CNC machining beginners should start by machining simple, basic designs before attempting complex tasks. This helps build confidence in using CAD/CAM software, setting up the workpiece, and selecting appropriate cutting tools.
Learn G-Code and CAM Software Basics
Even if the machine is automated, familiarizing yourself with the programming language for CNC machines and CAM software is essential. You may also need to understand CNC machine codes, particularly the geometric code (G-code), which enables you to control the machine and adjust its functionalities. Even at that, you may need to understand the miscellaneous codes (M-codes), which focus on the machine’s non-geometric functions. Generally, a strong foundation in programming will improve your confidence and ability to handle CNC machines. It will also enhance problem-solving skills when adjusting tool paths or troubleshooting issues.
Trial Runs and Demonstrations
Before machining an actual part, it’s advisable to run simulations or dry runs to identify potential errors. Some CNC software includes virtual machining environments to preview the toolpath before you CNC machine the material.
Optimize Tooling and Workholding
Proper tool selection and work holding setup directly impact precision and efficiency. Beginners should familiarize themselves with end mills, drill bits, lathe tool inserts, and clamps to prevent vibrations or material displacement during machining.
Understand Machine Speeds and Feeds
Incorrect machining parameters, such as the spindle speeds and feed rates, can significantly alter your machining tasks. If not optimized, it may even result in tool breakage or poor surface finishes. As a result, new users must optimize machining performance to suit their project. You can start by referencing the manufacturer’s guidelines.
Support and After-Sales Services
Checking for technical support, maintenance services, and training programs is crucial for those purchasing CNC machines from a supplier. Beginners can also benefit from online communities, forums, and workshops to learn troubleshooting techniques.
Maintain and Inspect the Machine Regularly
Routine maintenance—such as lubricating moving parts, cleaning chips, and checking spindle alignment—prevents unexpected breakdowns. Developing good machine care habits ensures a longer lifespan and consistent machining quality.
Conclusion
CNC milling and turning have distinct advantages depending on design complexity, material type, and production volume. Before deciding, beginners must assess their project needs, budget, and training requirements. In addition, starting with simple projects, optimizing tooling, and leveraging support services can significantly enhance machining efficiency.
By understanding these factors and applying practical tips, new users can confidently choose the right CNC machine and improve their machining capabilities. Whether for prototyping or full-scale production, selecting the proper CNC process ensures precision, efficiency, and long-term success in manufacturing.